Predictive Maintenance
Predictive Maintenance
With the rapid advancement of network technologies and sensors, monitoring sensor data such as pressure, temperature, current, vibration and other electrical variables has become much more important. With advances in big data and artificial intelligence, solutions can be developed to prevent breakdowns and predict the remaining life of equipments.
Predictive maintenance systems use historical data to improve fleet efficiency, advising fleet managers not only on what their vehicles are doing, but what they should do in the future. Different equipment performs different tasks and therefore has different needs. Predictive maintenance can help identify which equipment needs more regular maintenance and which problems may occur frequently. Compared to routine or time-based preventive maintenance, this approach offers cost savings because maintenance is predictive and performed as needed.


How Does It Predict the Future?
By collating historical data through software, malfunction patterns are analyzed, and future malfunctions are predicted. Predicting future malfunctions and real-time monitoring of the system allows maintenance to be planned before a malfunction occurs.
Parameters Expected to be Predicted
- Brake pad wear
- Oil changes
- Tire rotations, wheel realignments
- DPF (diesel particulate filter) clogging
- Tire pressure
- Fuel tank temperature
- Fuel tank level
- Temperature and pressure of engine oil and coolant (oil change requirements)
- Engine speed
- Battery voltage and temperature
- Correlations, predicting new malfunctions from similar ones
- Bilgi Güvenliği Politikası
- Tedarikçi İlişkileri Politikası
- Kişi Tespit Bilgisinin Mahremiyeti ve Korunması Politikası
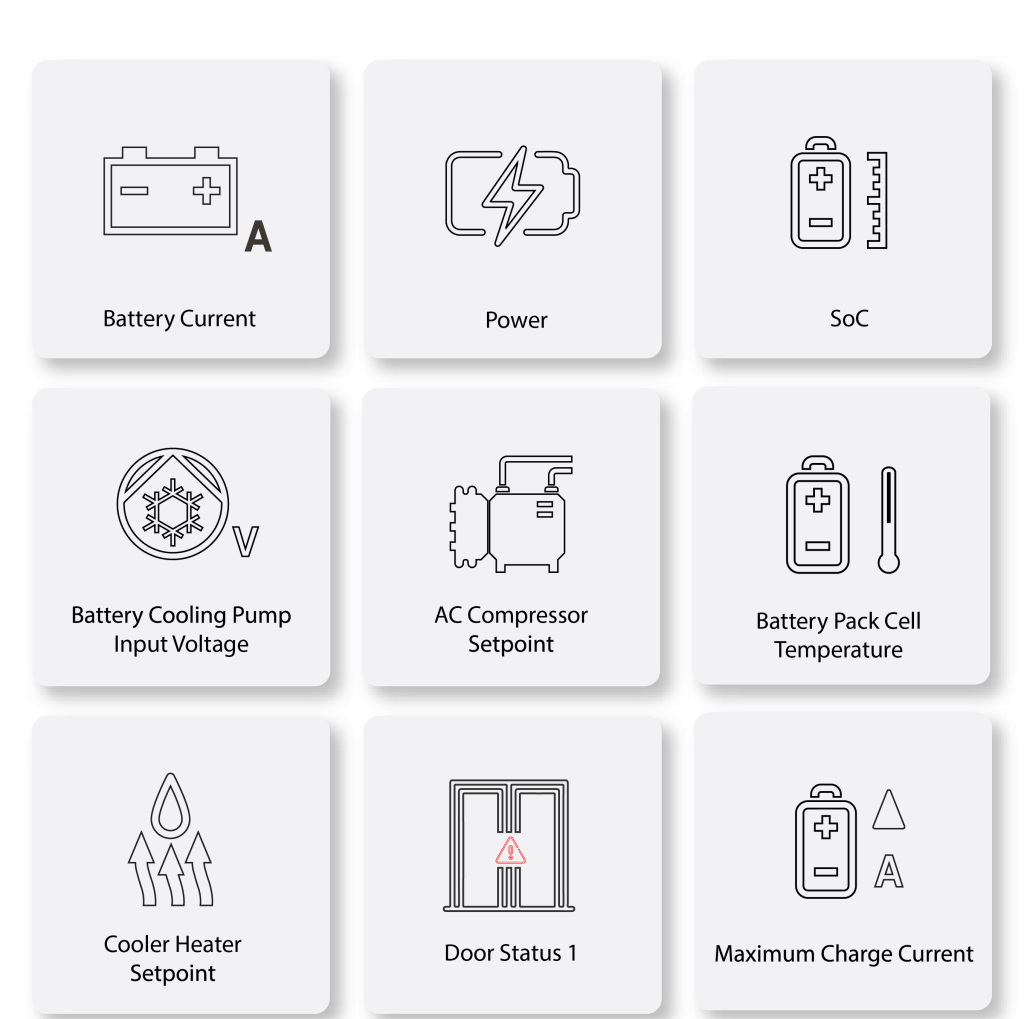